Additive Manufacturing and High-Purity Indium: 3D Printing in Electronics
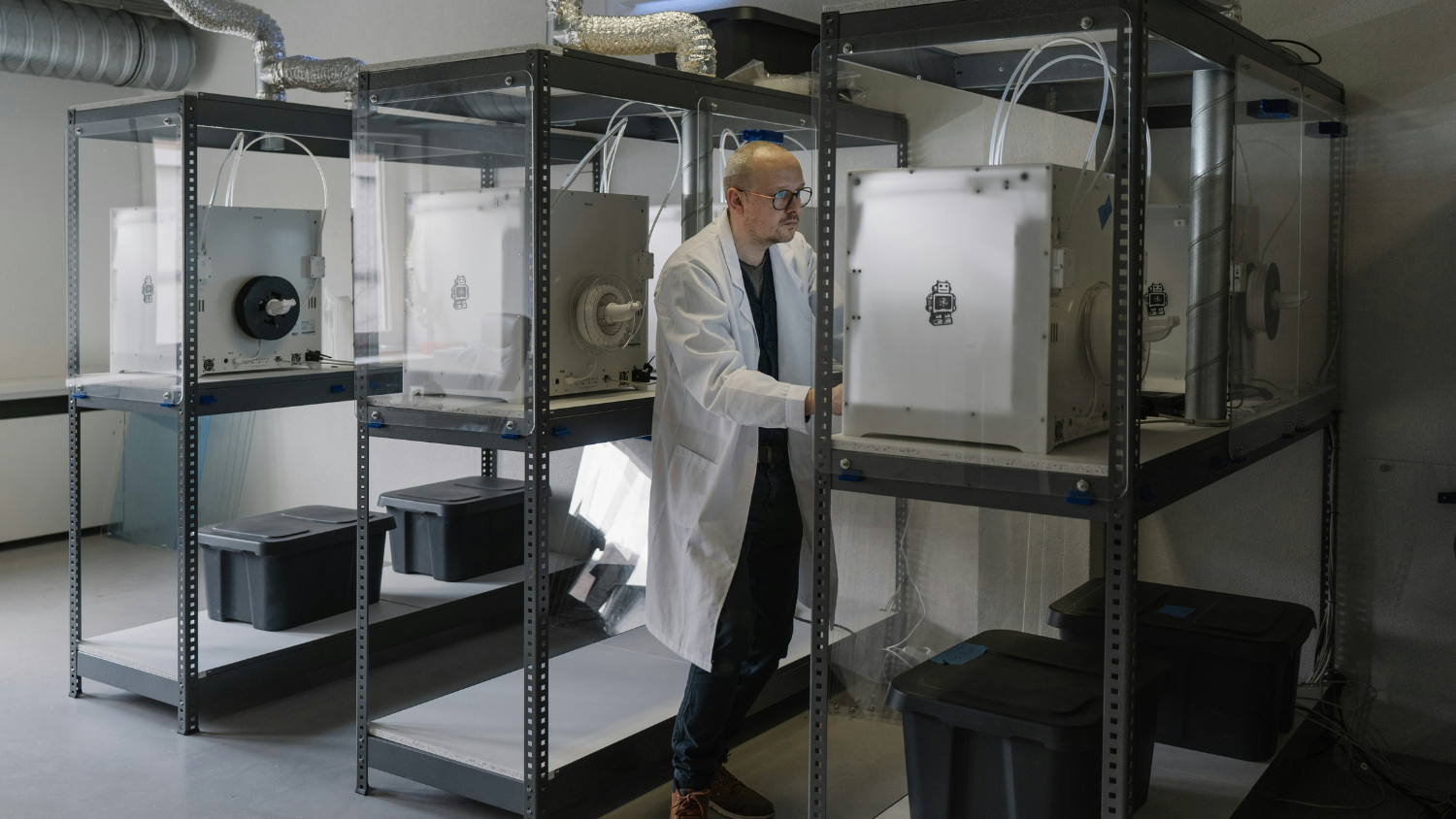.png?width=50)
Additive manufacturing is the process of creating an object by building it one layer at a time.
It is the opposite of subtractive manufacturing, in which an object is created by cutting away at a solid block of material until the final product is complete. Today it typically refers to 3-D printing.
High-purity indium, with its unique properties, is increasingly being leveraged in metal 3D printing to produce precise electronic components. This advancement is not only enhancing the capabilities of 3D printing but also expanding its applicability to sophisticated electronic systems.
High-purity indium, typically classified as 5N (99.999%) or higher, is a soft metal with exceptional thermal and electrical conductivity.
It is used predominantly in the manufacturing of compound semiconductors, soldering applications, and more recently, as a material in additive manufacturing.
The reason high-purity indium is gaining traction in 3D printing is due to its malleability, low melting point (156.6 °C) and the ability to form alloys that are highly conductive. These properties are crucial when creating intricate and precise components that require efficient electrical pathways, such as in microelectronics and power devices.
Additive manufacturing using high-purity indium is proving advantageous for a number of electronic applications, particularly in the production of customised, small-batch components where high precision is required.
Unlike traditional subtractive methods, which involve removing material to achieve the desired form, additive manufacturing allows for the layer-by-layer construction of parts. This precise layering makes it possible to produce complex geometries that would be challenging or even impossible using traditional manufacturing techniques.
For instance, high-purity indium has been successfully used in 3D printing to create conductive interconnects in flexible electronic devices. Flexible electronics, such as those found in wearable technology or medical sensors, benefit greatly from the unique combination of flexibility and electrical conductivity that indium offers. Furthermore, the ability to precisely deposit indium during the printing process ensures the integrity and reliability of these interconnects, which is critical in electronic applications where signal transmission stability is paramount.
Applications in Electronics
The use of high-purity indium in additive manufacturing also extends to the production of thermal interface materials (TIMs). These materials are essential in power electronics to ensure efficient heat dissipation from high-performance components. 3D printing allows for the precise placement of indium-based TIMs, enabling enhanced thermal management solutions that are customised for specific devices. This approach is particularly beneficial for applications like power semiconductors, where managing heat is crucial to maintaining performance and longevity.
In addition, 3D printing of indium alloys is being explored for advanced semiconductor packaging, where indium’s properties contribute to improved thermal and electrical performance. Semiconductor packaging, such as 2.5D and 3D packages, often requires materials that can bridge micro gaps and maintain conductivity under thermal stress. Indium's ability to do so, coupled with the flexibility offered by additive manufacturing, makes it an ideal choice for these high-performance applications.
The Future of High-Purity Indium in 3D Printing
Looking ahead, the role of high-purity indium in additive manufacturing is expected to grow as new techniques and applications are developed. Research is currently underway to optimise the deposition methods for indium to improve layer adhesion and material utilisation efficiency. Innovations in laser sintering and electron beam melting are making it possible to further refine the use of high-purity indium in 3D printing processes, thereby enhancing the precision and reducing material wastage.
Moreover, as industries continue to demand more complex and miniaturised electronic components, high-purity indium’s role in additive manufacturing will become increasingly central. Its ability to produce finely detailed, conductive pathways with minimal thermal resistance is unmatched, making it indispensable in fields ranging from consumer electronics to aerospace systems.
The integration of high-purity indium in additive manufacturing marks a significant advancement for the electronics industry. Its unique properties—excellent thermal and electrical conductivity, low melting point, and malleability—make it well-suited for producing complex, precise components in various electronic applications.
From enhancing the thermal management of power semiconductors to creating reliable conductive pathways in flexible electronics, high-purity indium is proving to be a versatile and valuable material in the world of 3D printing. As technologies evolve, the demand for efficient, customisable, and high-performance electronic components will only grow, and high-purity indium will undoubtedly play a pivotal role in meeting these needs.
For more information on high-purity indium and how Advent Research Materials can support your additive manufacturing needs, please contact us today.