Inconel 400® and 600®: Built for Tough Environments
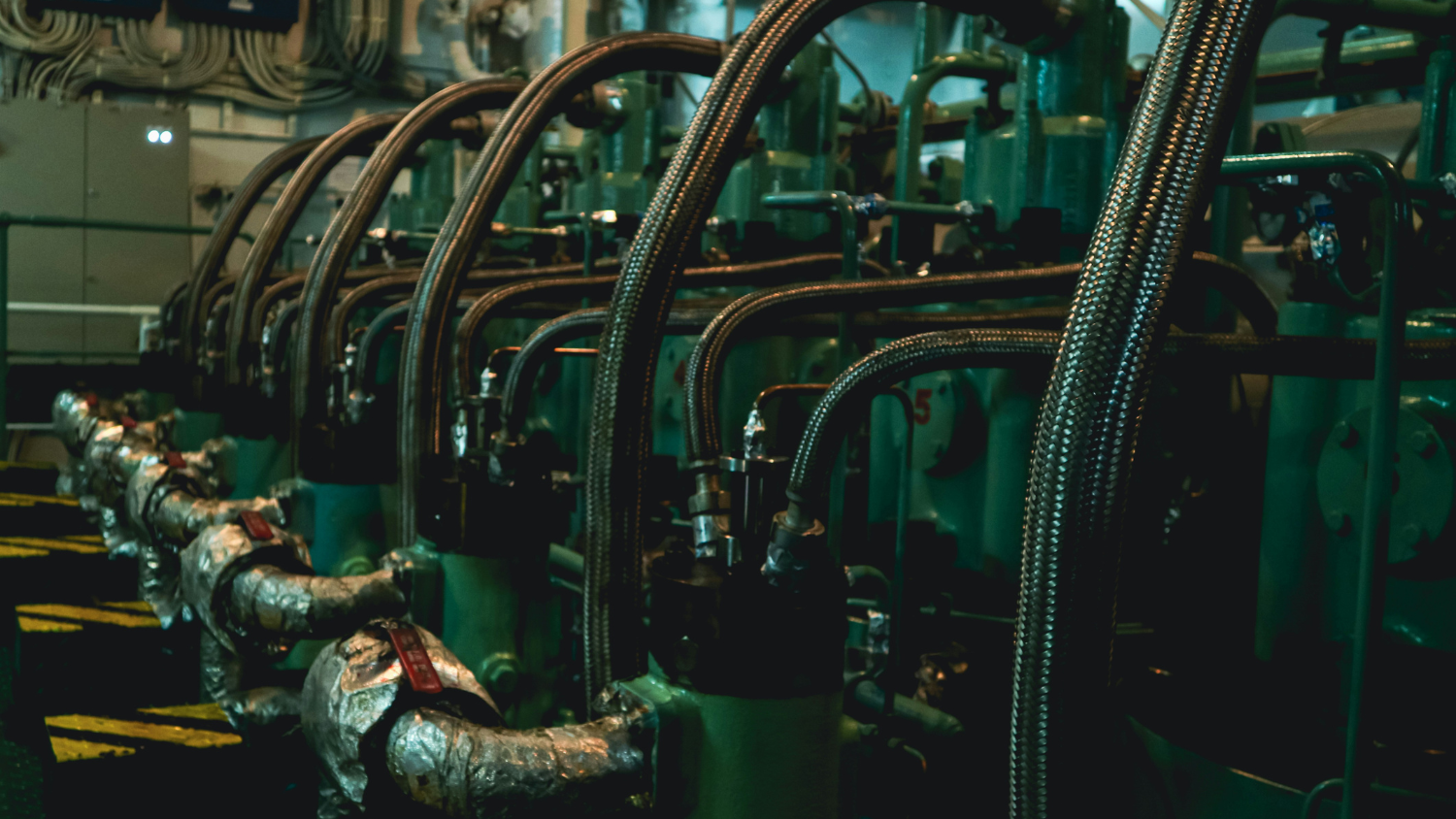.png?width=50)
Both Inconel 400® and 600® belong to the family of nickel-based alloys. They share a reputation for outstanding resistance to corrosion and high-temperature stability, yet each has distinctive features that make it suitable for particular applications.
Inconel 400® contains a high nickel content, complemented by copper. It is particularly known for its excellent resistance to hydrochloric and sulfuric acids, as well as stress corrosion cracking in freshwater environments.
Inconel 600®, composed primarily of nickel and chromium, is highly resistant to oxidation and carburisation, even at extreme temperatures. This makes it a popular choice in high-heat applications.
Inconel 400®
Particularly valued in sectors where exposure to corrosive environments is unavoidable, ts ability to resist chemical attack and maintain integrity under demanding conditions makes it a preferred choice for many challenging applications including;
- Marine Applications: In marine engineering, Inconel 400® is used in saltwater applications like propeller shafts and seawater piping, where it resists the corrosive effects of chloride ions. Its durability also makes it ideal for marine fasteners, valves, and fittings.
- Chemical and Petrochemical Processes: In chemical and petrochemical processing, Inconel 400® is employed in equipment exposed to sulfuric and hydrofluoric acids. Heat exchangers, distillation columns, and reaction vessels benefit from its corrosion resistance and longevity.
- Energy Sector: In the energy sector, Inconel 400® plays a role in nuclear reactors, where its high-temperature corrosion resistance is crucial. It also supports renewable energy systems, such as geothermal energy extraction.
Inconel 600®
- Aerospace: In aerospace engineering, Inconel 600® is found in jet engines and aircraft components, where it withstands high temperatures without losing strength. Its resistance to creep deformation makes it ideal for turbine blades and exhaust systems.
- Nuclear: In the nuclear industry, Inconel 600’s oxidation resistance ensures reliability in reactor components. It performs exceptionally well in environments exposed to both heat and radiation.
- Chemical Processing: In chemical processing, Inconel 600® maintains stability under fluctuating thermal conditions, making it suitable for heat exchangers and evaporators.
- Furnaces: For furnace components, Inconel 600’s ability to endure extreme heat makes it a preferred material for rollers, radiant tubes, and other heating elements.
Why Advent Research Materials?
Advent Research Materials provides high-quality Inconel 400® and 600® to meet the demands of cutting-edge research and development applications.
Whether you’re working in aerospace, marine, or energy production, our extensive inventory and expertise ensure you receive the right material for your project.
With a commitment to delivering excellence, Advent is the trusted partner for your research and development needs.
Inconel 400® and 600® are indispensable for industries requiring materials that perform reliably under extreme conditions.
From chemical processing plants to aerospace applications, these alloys provide the strength, corrosion resistance, and durability needed to tackle the toughest challenges.
If your project demands materials that excel in demanding environments, Advent Research Materials is ready to support you with the expertise and quality you can trust.